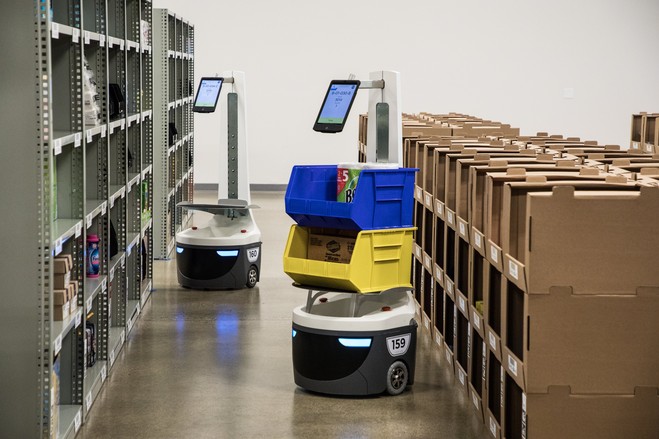
Lately, robots are turning up more on factory floors and assembly lines, as companies struggle to hire enough workers to fill the rising orders. Workplace robot orders jumped by 40% this year’s first quarter in the U.S. Robot orders priced at $1.6 billion, climbed by 20% in 2021 following years of stagnant declining order volumes.
The adoption of robots in companies was caused by certain challenges such as rising wages and employee shortages, compounded by the increase in covid-19 related absenteeism which is already altering some producers’ attitudes about robotics.
Some companies misplaced about 40% of their manufacturing days during the peak of the covid-19 pandemic which affected their workforce. Such disruption prompted a few companies to add extra robots to the workforce.
Tekedia Mini-MBA edition 16 (Feb 10 – May 3, 2025) opens registrations; register today for early bird discounts.
Tekedia AI in Business Masterclass opens registrations here.
Join Tekedia Capital Syndicate and invest in Africa’s finest startups here.
Despite the ease of the covid-19 virus, some companies have decided to stick with the use of robots which according to them has already brought about a positive paradigm shift in the workplace and companies. In North America, the use of commercial robots has for years been concentrated within the automotive trade.
While automakers and producers of auto elements accounted for 71% of robotics in 2016, robots have also made inroads into different sectors, such as the manufacturing sector (manufacturing meals), the Health sector (prescription of drugs), and shopper merchandise. Executives of such companies revealed improved capabilities as they will therefore permit robots to be programmed for more complex duties.
Most executives have also revealed the positive impacts of the use of robots in their companies, where a task that usually takes a worker about three hours to finish, takes a robot about half an hour which has no doubt saved time and improved production outputs.
According to analysis firm Oxford Economics, it disclosed that up to 20 million manufacturing jobs around the world would be replaced by robots in 2030. Each new industrial robot wipes out about 1.6 manufacturing jobs.
It has been estimated that regions where people have lower skills, which tend to have weaker economics and higher unemployment rates, are more vulnerable to the loss of jobs. Some workers in the manufacturing companies, out of fear of displacement, have left their jobs with so many others considering leaving.
Some of these workers move to sectors like transport, construction, administrative offices, etc. Unfortunately, what they fail to understand is that in this 21st century where everything is rapidly evolving, a lot of jobs are vulnerable to automation. What these workers need is to arm themselves with on-demand skills to ensure that they are not jobless in case they are replaced with robots. Jumping from one job to another is unreasonable and it doesn’t guarantee job security.
The world is evolving and a vast majority of people, even those with jobs are beginning to see the importance of having necessary on-demand skills. There have been plenty of productions that robots are going to displace, a lot of jobs ranging from factory workers to white-collar jobs which are vulnerable to automation are going to be replaced with robots.
With the rise of robotics, it is expected that the job market will change significantly. Much of the administrative work in the workplace will be automated, which will therefore change the scope of administrative employees.
With nearly 3 in 4 global companies investing in automated tech, the trend is already frightening for many employees. In this 21st century where a lot of advancements are already taking place, the ideal thing for anyone to do, even those with jobs, is to properly arm themselves with necessary skills, because the change from employees to robots is very imminent and would definitely displace a lot of workers.