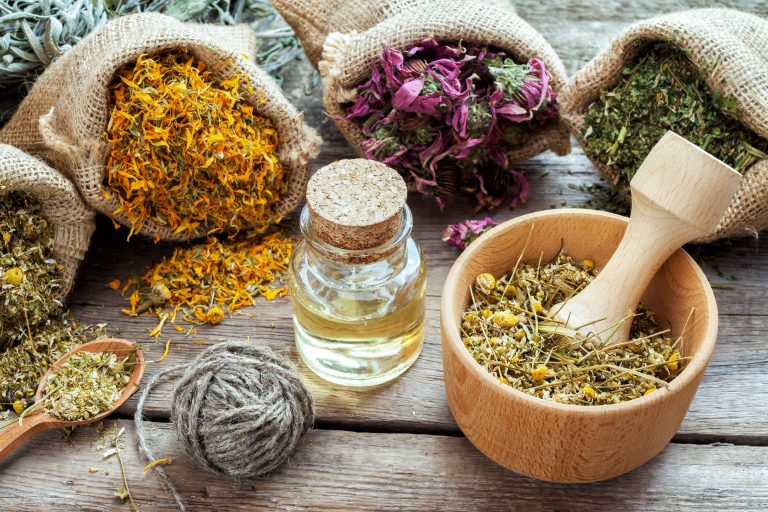
Herbal medicine is increasingly coming into the mainstream of healthcare, and with their increasing acceptance and consumption, comes a high rate of risks which require a higher amount of regulatory checks , especially in Nigeria.
The objective of the Manufacturing Guidelines for Herbal Medicinal Products as outlined by the National Agency For Food and Drug Administration and Control (NAFDAC) is to ensure that products are consistently manufactured in conformance with quality standard.
The NAFDAC guidelines are concerned with all aspects of production and quality control of Herbal Medicinal Products.
Tekedia Mini-MBA edition 16 (Feb 10 – May 3, 2025) opens registrations; register today for early bird discounts.
Tekedia AI in Business Masterclass opens registrations here.
Join Tekedia Capital Syndicate and invest in Africa’s finest startups here.
These guidelines are for the manufacture and storage of Herbal Medicinal Products.
It is necessary to emphasize that, no Herbal Medicinal Product should be manufactured, exported, advertised, sold or distributed in Nigeria unless it has been registered in accordance with the provisions of the Food, Drugs and Related Products Act Cap F33 LFN 2004 (formerly decree 19 of 1993) and the accompanying guidelines.
These guidelines cover the quality aspects of the product, but do not cover safety aspects for the personnel engaged in the plant, nor protection of the environment. Safety and environmental aspects are inherent responsibilities of the company and should be governed by National legislation and regulations.
These guidelines are not applicable to research and development activities of finished Herbal Medicinal Products.
Good Agricultural and Collection Practice and Good Herbal Processing Practice which is a complement of Good Manufacturing Practice should be practiced in the various processing (primary, secondary or special) of the starting materials through the herbal preparation and/or herbal dosage forms of finished Herbal Medicinal Products and should precede Good Manufacturing Practice.
It should be noted that the manufacture of Herbal Medicinal Products of sterile origin (infusion, ophthalmic, solution, injectable, implants etc.) is beyond the scope of this guideline.
Definition of Terms
For the purposes of this document, the following terms and definitions apply.
–Audit:- Systematic and independent examination to determine whether quality activities and related results comply with planned arrangements and whether these arrangements are implemented effectively and are suitable for achieving objectives.
–Batch:- a quantity of any herbal product produced in a given cycle of manufacture that is uniform in character and quality.
–Batch Number :- a designation in numbers and/or letters or combination of both that identifies the complete history of the batch, quality control and distribution.
–Bulk Product:- any processed product, which will have to undergo the packaging operation in order to become a finished product.
–Calibration:- combination of checking an instrument and adjusting it to bring it within its limits for accuracy according to recognized standards.
–Cleaning:- all operations that ensure a level of cleanliness and appearance, consisting of separating and eliminating generally visible dirt from a surface by means of the following combined factors, in variable proportions, such as chemical action, mechanical action, temperature, duration of application.
–Complaint:- external information claiming a product does not meet defined acceptance criteria.
– Contamination:- occurrence of any undesirable matter such as chemical, physical and/or microbiological matter in the product.
–Contract acceptor:-person, company or external organization carrying out an operation on behalf of another person, company or organization.
–Contract giver:- person, company or external organization that contracts out an operation to another person, company or organization.
–Control:- verification that acceptance criteria are met.
–Documentation: all written procedures, instructions and records involved in the manufacture and quality control of products.
–Finished Herbal Products/Herbal Medicinal Product:- a product, containing as active substances exclusively herbal drugs or herbal preparations. They may consist of herbal preparations made from one or more herbs. If more than one herb is used, the term mixed herbal product can also be used. They may contain excipients in addition to the active ingredients. It may contain by tradition, natural organic and inorganic active ingredients, which are not of plant origin (e.g. animal materials and mineral materials). Generally, however finished products or mixed products to which chemically defined active substances have been added, including synthetic compounds and/or isolated constituents from herbal materials, are not considered to be herbal medicinal products.
GENERAL CONSIDERATIONS
-In the manufacture of herbal medicinal products, monitoring is essential in ensuring that products of quality standards are produced.
-Unlike conventional pharmaceutical products, which are usually produced from synthetic materials by means of reproducible manufacturing techniques and procedures, herbal medicines are prepared from materials of herbal origin, which are often obtained from varied geographical and/or commercial sources. As a result it may not always be possible to ascertain the conditions to which they may have been subjected.
-In addition, they may vary in composition and properties. Furthermore, the procedures and techniques used in the manufacture and quality control of herbal medicines are often substantially different from those employed for conventional pharmaceutical products.
-Because of the inherent complexity of naturally grown medicinal plants and the often variable nature of cultivated ones, the examples of contamination with toxic medicinal plants and/or plant parts and the number and small quantity of defined active ingredients, the production and primary processing has a direct influence on the quality of herbal medicines. For this reason, application of GMPs in the manufacture of herbal medicines is an essential tool to assure their quality.
PERSONNEL
General Considerations
-There should be sufficient number of personnel with adequate knowledge, experience, training and education relevant to their assigned functions.
-The responsibilities placed on any one individual should not be so extensive as to present any risk to the product.
– Key personnel i.e. persons responsible for production and quality control, must be employed on full time basis.
-Personnel specific duties should be recorded in individual job descriptions and personnel should be given adequate authority to carry out their responsibilities.
-Duties may however be delegated to designated deputies with satisfactory qualification and practical experience.
-All personnel should be responsible for the establishment and maintenance of high quality standards.
-Experts in the different areas of interest in herbal medicine manufacturing may be engaged upon documented confirmation of their education, training or experience in their areas of proficiency.
Organization, Qualification and Responsibilities
-The organizational structure of the company should be such that different persons head the production and quality control sections, neither of which should report to the other. The organizational structure should clearly state the reporting lines for all key personnel.
-The head of production should have the requisite training and experience as well as knowledge and understanding of practical problems encountered in the manufacturing of herbal medicinal products.
-The head of production should have authority and responsibility to manage production; covering operations, equipment, production personnel, production areas and records.
-The head of quality control should have full authority and responsibility for all quality control duties such as establishment, verification and implementation of all quality control procedures. He should have the authority to approve or accept starting materials, intermediates, bulk and finished products that meet specification or to reject those which do not conform or those not manufactured in accordance with approved procedures.
-Where necessary, the quality control activities could be outsourced with an agreement drawn to outline specific roles of concerned parties.
PREMISES
-The premises for manufacturing should be suitably located, designed, constructed and maintained to suit the operations to be carried out and facilitate good sanitation and hygiene.
-Effective measures should be taken to avoid any contamination from the surrounding environment and from pests.
-Painted line, flexible barrier in the form of mark or tape may be employed to prevent mixups.
-Appropriate change rooms and facilities should be provided. Toilets should be separated from the production areas to prevent product contamination/cross contamination.
At a minimum, defined areas should be provided for:
-Materials receiving bay.
-Incoming goods quarantine.
-Starting materials storage.
-Packaging materials storage.
-Processing and packaging operations.
– Storage of finished products.
-Laboratories (where available).
-Rejected materials and products.
-Returned and recalled products.
-Walls and ceilings should be smooth and easy to maintain. The floor in processing areas should have a smooth surface, easy to clean and disinfect and be made of non-slippery material.
-Drains in processing areas should be of adequate size and should not allow backflow. Open drains outside the processing areas should be avoided, but if required they should facilitate cleaning and disinfection.
-Buildings should be adequately lit and properly ventilated. Lighting points should flush with the ceiling and windows should flush with the walls.
-Pipework, light fittings, ventilation points and other service points in manufacturing areas should be installed in such a way to make for easy cleaning.
-Laboratories (where available) should be separated from the production areas.
Storage Areas.
-Storage areas should be of sufficient capacity to allow orderly placement of materials such as starting and packaging materials, bulk and finished products, products in quarantine, released, rejected, returned or recalled products.
-Precautions should be taken to prevent herbal materials, preparations and finished products from degradation and infestation with pests as well as biological contamination. Where applicable, special conditions of humidity, temperature and light protection should be provided for storage of plants, extracts, tinctures and other preparations.
-The premises should be so constructed as to provide maximum protection for the starting materials, packaging materials and finished herbal products against birds, insects, rodents as well as domestic animals.
– Incoming fresh herbal materials should be processed, unless specified otherwise, as soon as possible; or appropriately at the required temperature, humidity or light.
-For materials stored in bulk, liability to mould formation or fermentation could arise. Such materials should be stored in aerated rooms or containers using natural or mechanical aeration and ventilation.
-Wherever possible, sampling area for starting materials should be provided to prevent contamination
EQUIPMENT
Construction and Design
– Manufacturing equipment should be designed and constructed to suit manufacture of the product.
-The equipment surfaces in contact with starting material, in-process material and finished product should not react with or adsorb the materials being processed.
– Equipment should not adversely affect the product through leaking valves, lubricant drips and inappropriate modifications or adaptations.
-Equipment should permit effective cleaning, avoid dust or dirt build up and any adverse effect on the quality of products.
-Equipment should be closed or contained for intended usage. Where open equipment is to be used, precautions should be taken to prevent the risk of contamination.
-Non-wooden equipment should be used unless tradition demands the use of wooden material. Where it is necessary to use traditional equipment (such as wooden implements, clay pots, pallets, hoppers, etc.), these should be dedicated per product/material unless otherwise justified.
Installation and Location
-Equipment should be located to avoid congestion and permit free movement of man and material.
-Equipment should be properly identified using identification numbers to assure that products do not become admixed or confused with one another.
-Measures to assure protection of personnel, products and environment should be put in place.
Maintenance of Equipment
-Weighing, measuring, testing and recording equipment should be checked and calibrated regularly and all records of such activities should be maintained.
-Where applicable, calibration of equipment should be performed using standards traceable to certified standards and a calibration label affixed to such .
-Measuring instrument that do not meet calibration criteria or whose calibration date has expired should not be used but labelled “not permitted for use”.
SANITATION AND HYGIENE
-Sanitation and hygiene should be practiced to avoid contamination of products. It should cover personnel, premises, equipment, production materials and containers.
Quality Control Specifications
-All specifications should be approved by the Quality Control personnel.
-Raw and packaging material specifications should include:
-Name of material
-Description of the material
-Testing parameters and acceptance limits
Storage and Safety Conditions.
Bulk and finished product specifications should include:
-Name of product
-Description of product
-Physical properties of the product
-Chemical assay and/or microbiological assays and their acceptance limits
-Storage conditions and safety precautions.