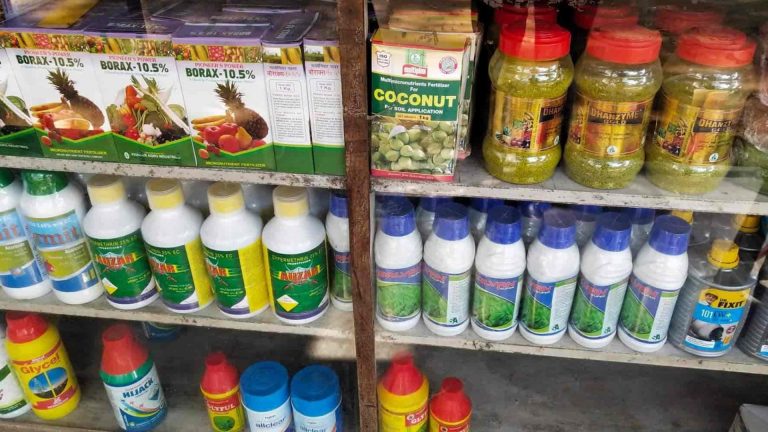
The objective of the regulatory framework governing Chemical Good Manufacturing Practice (GMP) guidelines as issued by the National Agency For Food and Drug Administration and Control (NAFDAC) is to ensure that products are consistently manufactured in conformance with quality standard. It is concerned with all aspects of production and quality control.
These guidelines are for the manufacture, storage, distribution and shipment of chemicals and chemical products in Nigeria.
It is necessary to emphasize that, no chemical products shall be Manufactured, Exported, Advertised, Sold or Distributed in Nigeria unless it has been registered in accordance with the provisions of the Food, Drugs and Related Products Act Cap F33 LFN 2004 (formerly decree 19 of 1993) and the accompanying guidelines. The provisions of these guidelines regarding chemicals and chemical products are what will constitute the focus of this article.
Tekedia Mini-MBA edition 16 (Feb 10 – May 3, 2025) opens registrations; register today for early bird discounts.
Tekedia AI in Business Masterclass opens registrations here.
Join Tekedia Capital Syndicate and invest in Africa’s finest startups here.
What are the general considerations highlighted by the NAFDAC guidelines on chemicals?
In the manufacture of chemicals and chemical products, monitoring is essential in ensuring that products of quality standards are produced.
Provisions of the guidelines on personnel
-There should be adequate number of personnel with adequate knowledge, experience, skill and capabilities relevant to their assigned function. They should be in good health and capable of handling the duties assigned to them.
Provisions of the guidelines on organization, qualification and responsibilities
-The organizational structure of the company shall be such that different persons head the production and quality control sections, neither of which shall be responsible to the other.
-The key officers should have a minimum qualification of BSc or equivalent in Chemistry/Chemical Engineering or any related science disciplines.
-The head of production should be adequately trained, experienced and qualify in chemical manufacturing. He/she should have authority and responsibilities to manage production; covering operations, equipment, production personnel, production areas and records.
-The head of quality control should be adequately trained and experienced in the area ofquality control. He should have full authority and responsibility in all quality control duties such as establishment, verification and implementation of all quality control procedures. He should also have the authority to designate/assign when appropriate,personnel, to approve starting materials, intermediates, bulk and finished products that meet specification or to reject those which do not conform or not manufactured in accordance with approved procedures.
-The responsibilities and authorities of key personnel should be clearly defined.
Training
-All personnel directly involved in manufacturing activities should be appropriately and continuously trained in manufacturing operations in accordance with GMP principles. Special attention should be given to training of personnel working with hazardous materials.
-Records of training should be maintained and its effectiveness assessed periodically.
Premises
-The premises for manufacturing should be suitably located, designed, constructed and maintained.
-Effective technical and administrative measures should be taken to avoid any cross contamination to the environmentand the production facility.
-Appropriate changing rooms and toilet facilities should be provided.
-Defined areas should be provided for, wherever possible and applicable:-
a).Materials receiving bay
b). Material Sampling
c).Incoming goods and quarantine.
d).Starting materials storage.
e).Weighing and dispensing.
f). Processing.
g). Storage of bulk products.
h). Packaging
i). Quarantine storage before final release of products.
j). Storage of finished products.
k).Loading and unloading.
l). Laboratories.
m).Equipment washing.
-Walls and floors, where applicable should be smooth and easy to maintain. The floor in processing areas should be industrial concrete floor with surface that is easy to clean.
-Drains should be of adequate size and have trapped gullies and proper flow. Open channels should be avoided where possible, but if required they should be able to facilitate cleaning and disinfection.
-Buildings should be adequately lit and properly ventilated.
-Pipework, light fittings, ventilation points and otherservice points in manufacturing areas should be installed in such a way to make for easy cleaning.
-Laboratories should be separated from the production areas. The premises for manufacturing should be suitably located, designed, constructed and maintained.
Storage Areas
-Storage areas should be of sufficient capacity to allow orderly placement of materials such as starting and packaging materials, intermediates, bulk and finished products, products in quarantine, released, rejected, returned, or recalled products.
-Secured segregated area should be available for storage of chemicals of safety and security concerns.
-Storage areas should have good storage conditions. Where special storage conditions are required (temperature, humidity and security) these should be provided, checked and monitored
Provisions of guidelines on Equipment
Constructions and Design
-Equipment should be designed and constructed to suit production of the product.
-The equipment surfaces in contact with any in-process material should not react with or adsorb the materials being processed.
-Equipment should not adversely affect the product through leaking valves, lubricant drips and inappropriate modifications or adaptations.
-Equipment should be easily cleaned.
-Equipment used for flammable substances should be explosion proof.
Installation and Location
-Equipment should be located to avoid congestion and should be properly identified to assure that products do not become admixed or confused with one another.
-Support systems such as heating, ventilation, air conditioning (HVAC), steam, compressed air and gases should function as designed and identifiable.
Maintenance of Equipment
– Weighing,measuring, testing and recording equipment should be serviced andcalibrated regularly. All records should be maintained.
Sanitation and Safety
-Sanitation and safety should be practiced to cover personnel, premises, equipment, production materials and containers.
Personnel
-Personnel engaged in the manufacture, processing, packaging, or holding of chemical andchemical products should wear appropriate personnel protective equipment for assigned duties.
-Personnel should be healthy to perform their assigned duties. Regular medical examination should be conducted for all production personnel.
-Factory wears should not be worn out of the area they are meant for.
Premises
– Adequate employee’s washing and toilet facilities should be provided and separated from the production area.
-Suitable locker facilities should be provided at appropriate location for the storage of employee’s clothing and personal belongings.
Waste materials should be regularly collected in suitable receptacles for removal to collection points, outside the production area.
– Restricted areas to unauthorized personnel should be clearly defined with signage displayed appropriately.
PRODUCTION
Verification of Materials
-All deliveries of raw materials and packaging materials should be checked and verified for conformity to specifications and should be traceable to the product.
-Samples of raw materials should be physically checked for conformity to specifications priorto release for use. The raw materialsshould be clearly labeled. All goods must be clean and checked for appropriate protective packing to ensure no leakages, perforations or exposures.
Rejected materials
-Deliveries of raw materials that do not comply with specifications should be segregated anddisposed according to Standard Operating Procedures.
Batch Numbering System
-Every finished product should bear a production identification number, which enables the history of the product to be traced.
-A batch numbering system should be specific for the product and a particular batch number should not be repeated for the same product in order to avoid confusion.
-Whenever possible, the batch number should be printed on the immediate and outer container of the product.
– Records of batch number should be maintained.
Weighing and Measurement
-Weighing should be carried out in the defined areas using calibrated equipment.
-All weighing and measurement carried out should be recorded and where applicable, counterchecked.
Procedure and Processing
-All starting materials used should be approved according to specifications.
-All manufacturing procedures should be carried out according to written.
-All required in-process controls should be carried out and recorded.
-Bulk products should be properly labelled until approved by Quality Control, where applicable
Dry Chemical Products
– Handling dry chemical materials and products should be given special attention.
-Where possible, dust-containing production system, central vacuum system or other suitable methods should be employed.
Wet Chemical Products
-Liquid chemical products should be produced in such a way as to protect the product from spillage and other hazard contamination.
-Where pipelines are used for delivery of raw materials or bulk products, care should be taken to ensure that the systems are easy to clean.
Labeling and Packaging
-Packaging line should be inspected for clearance prior to operation.
-Equipment should be clean and functional. All materials and products from previous packaging operation should have been removed.
-Samples should be taken and checked at random during labeling and packaging operations.
-Each labeling and packaging line should be clearly identified to avoid mix-up.
-Excess labels and packaging materials should be returned to the store and recorded. Any rejected packaging materials should be disposed of accordingly.
Finished Product: Quarantine and Delivery to Finished Stock.
-All finished products should be approved by Quality Control prior to release.
Provisions of the guidelines on Quality Control
-Quality control is an essential part of GMP. It provides assurance that chemical products will be of consistent quality appropriate to intended use.
-A quality control system should be established to ensure that chemical products contain thecorrect materials of specified quality and quantity and are manufactured under proper conditions according to Standard Operating Procedures.
-Quality control involves sampling, inspecting and testing of starting materials, inprocess, intermediate, bulk, and finished products. It also includes where applicable, environmental monitoring programs, review of batch documentation, sample retention programs,stability studies and maintaining correct specifications of materials and products.