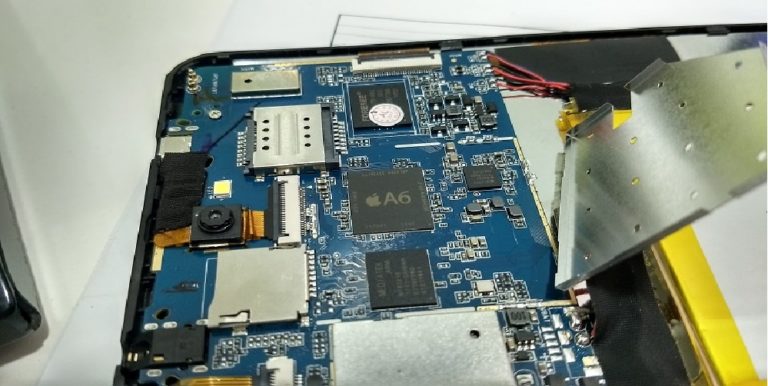
In the past, automation engineering was mainly understood as control engineering dealing with a number of electrical and electronic components. This picture has changed since computers and software have made their way into every component and element of communications and automation.
Advent of programmable controller
In automated industrial production line in the seventies, there was always a gigantic electrical board for system controls containing hundreds or thousands of relays, cam timers, and drum sequencers and dedicated closed-loop controllers. Electrician had to connect all relays manually using wires and engineer would design logic for the system, and electricians would receive a schematic outline of logic that they had to implement with relays. The plan that electrician was given was called “ladder schematic”.
Register for Tekedia Mini-MBA edition 17 (June 9 – Sept 6, 2025) today for early bird discounts. Do annual for access to Blucera.com.
Tekedia AI in Business Masterclass opens registrations.
Join Tekedia Capital Syndicate and co-invest in great global startups.
Register to become a better CEO or Director with Tekedia CEO & Director Program.
Ladder displayed all switches, sensors, motors, valves, relays, etc. found in the system. Since this is based on mechanical relays, the system breaks down frequently due to their moveable parts that could wear out. If one relay stopped working, electrician would have to examine an entire system which means the process would be of service until a cause of the problem was found and corrected.
The production has to be stopped so as to make connections on the electrical board. Assuming there are few errors from the engineer or technician, as systems are usually not perfect with a first try, finding errors would be a laborious process. Also products are not being made during these corrections and changes in connections period. Production line has to be stopped and that means the entire production staff in that line of production would be out of work until the system is fixed up. Expenditures for this kind of work are usually too much even for strong companies.
This brought the idea of replacing the system’s wired control board with a flexible, fast and easy to change automated line of production .The idea was to use microcomputer to replace system logic instead of wired relays. Computer could take place of gigantic, expensive, inflexible wired control boards. If changes were needed in system logic or in order of operations, program in a microcomputer could be changed instead of rewiring of relays.
It was clear that it is required that this new device has be based on old method ladder diagram, already known to technicians and programmed easily and maintained by electricians and technicians. Also, it is required that a new device be based on electronic instead of mechanical parts, to have flexibility of a computer and computer has to be replaced with a controller that can withstand industrial environment.
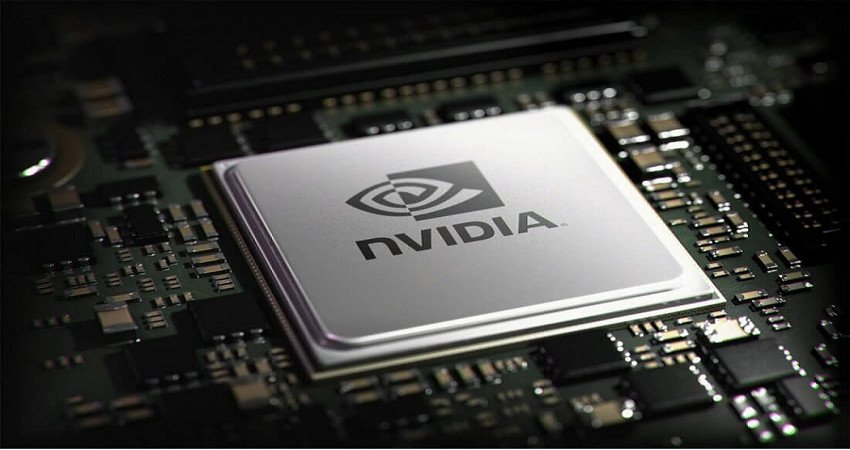
Composition of PLC controller
PLC is actually an industrial microcontroller system where you have hardware and software specifically adapted to industrial environment. Program unit is usually a computer used for writing a program (Ladder diagram) into the PLC. The main component of PLC are as follows;
Central Processing Unit – CPU: Is the brain of a PLC controller. CPU itself is usually one of the microcontrollers.
Memory: System memory (today mostly implemented in FLASH technology) is used by a PLC for process control. Aside from this operating system it also contains a user program translated from a ladder diagram to a binary form. Reprogramming a program memory is done through a serial cable in a program for application development.
Power supply: Most PLC controllers work either at 24 VDC or 220 VAC. User has to determine how much current to take from I/O module to ensure that electrical supply provides appropriate amount of current.
PLC controller inputs: Input signals can be logical (on/off) or analogue. Smaller PLC controllers usually have only digital input lines while larger also accept analogue inputs through special units attached to PLC controller.
PLC controller output: Output devices are motors, solenoids, relays, indicators, sound signalization and so on.
Extension lines: Every PLC controller has a limited number of input/output lines. If there is need, this number can be increased through certain additional modules by system extension through extension lines.
Programming a PLC controller: PLC controller can be reprogrammed through a computer or through manual programmers (consoles). This practically means that each PLC controller can programmed through a computer if you have the software needed for programming.