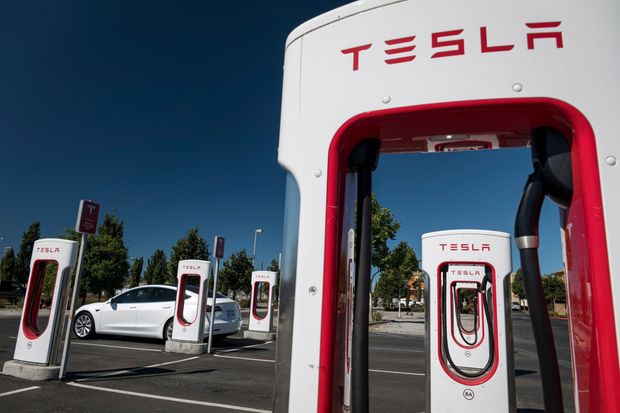
In production economics, three questions are important to finding the key to unlocking the market opportunities. First is what to produce, second is how to produce, and third is for whom to produce. These questions also guide the efficient use of scarce resources in bridging the demand and the supply gap. The flow of production resources from the supplier to the manufacturer through to the eventual delivery of the final products to the end-users is known as the supply chain.
Since companies want to optimize their cost, minimize risks of leakage and circumvent other complexities involved in getting their supplies and the flow of their products to the point of demand, they create structures that shape the dynamics of their supply chain and determine how efficiently they serve their customers.
One of such structures is the centralized supply chain model wherein all supply chain decisions, from procurement to distributions are centrally determined, usually from the headquarters. An alternative to this is the decentralized supply chain model which spreads decisions among a series of small units within the same business.
Tekedia Mini-MBA edition 16 (Feb 10 – May 3, 2025) opens registrations; register today for early bird discounts.
Tekedia AI in Business Masterclass opens registrations here.
Join Tekedia Capital Syndicate and invest in Africa’s finest startups here.
Unlike the decentralized model which usually involves too many stakeholders’ decisions; the centralized model is more responsive to change and adopted by companies that want to have firm control over their entire supply chain. Such comprehensive control enables firms to inwardly innovate and tailor their operation to the new market ordinance while still having a minimal operational cost and a higher profit margin.
The hiatus of the centralized model and that of the decentralized model are offset by a third model known as the hybrid model. The hybrid supply chain model is the fusion of both the centralized and the decentralized models.
A Case for Centralized Supply chain Model
Tesla is one of the leading brands in the automobile industry that centrally plans its supply chain operations. Founded in 2003, Tesla specializes majorly in electric vehicle production and is known for the aesthetics and long ranges of its electric vehicles. The company currently sells 4 fully electric vehicles (EV) models which includes; the model S sedan, the model X Sport Utility Vehicle (SUV) the model 3 and the model Y SUV through its own branded stores.
In September 2020, Elon Musk, Tesla’s founder and chairman, announced Tesla’s goal to build a US $25,000 mass-market electronic car and ramp up annual production to 20 million cars. In the year 2021, about 911,000 units of its Model 3 and model y were sold pushing the revenue base of the brand to $53 billion up from $31 billion in 2020. Since 2009 Tesla has produced 1.91 million electric vehicles. By 4Q2021, the brand’s market value already surpassed the $ 1 trillion dollar market cap. Tesla is able to achieve this great fit by having comprehensive control of its supply chain.
By centralizing some crucial elements of its supply chain, from resource procurement to product distribution and add-value services such as its self-reliant charging network, Tesla is able to enjoy economies of scale and efficiencies to improve performance, minimize cost and deliver a superior customer service experience. The company is also able to adapt changes to its customs manufacturing process, prevent patent loss and increase the speed of innovation, and have quick access to the market.
For example, while experts forecast that battery cost needs to come down to about 100 US Dollars per Kilowatt for EVs to witness mass adoption in the industry, Gigafactory, Tesla’s $ 5 billion battery production company in Nevada presents an interesting playbook that can reduce production cost by up to 35 percent by streamlining labour, time and transport. Thus, through Gigafactory, Tesla gets the best possible chance to reduce operational costs and still achieve maximum output. Also, Tesla’s in-house distribution channel gives it leverage to sell directly to the end-users through the company’s website and showrooms without having to incur extra costs from dealers’ mark-ups and excesses of investors.
Furthermore, where many of its competitors have had to endure production delays, suspend their models and increase prices due to ongoing semiconductors shortages in the industry, Tesla is able to navigate this shortfall more effectively through its unified computing architecture. By owning its own software, the company’s AI engineers were able to access, modify and rewrite the software according to their needs and thereby make use of available chips from other vendors.
Thinking Forward
A Supply chain model should be customer-centric and contingent upon changes within an industry. Whereas Tesla is scaling with its centralized supply chain model, other businesses in other industries may find the alternative models more expedient to the peculiarities of their supply chain ecosystem. Understanding these dynamics informs the efficiency of the scarce resources used in bridging the supply-demand gap.
References:
Statista. April 2022. Insights on the competitive landscape in eMobility