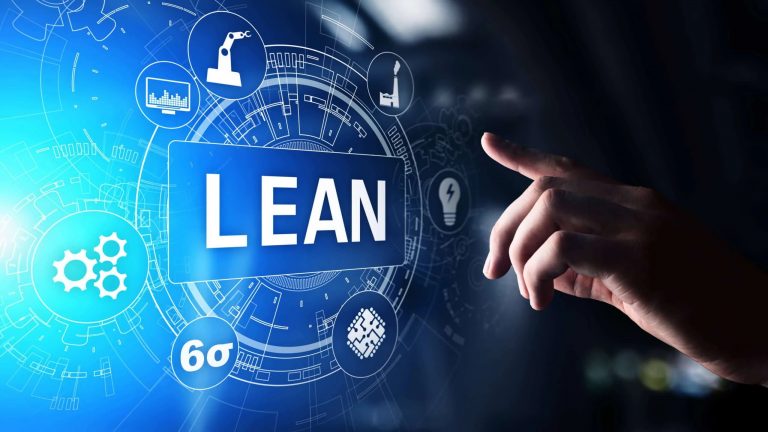
Achieving results by minimizing waste and maximizing value has become quite trendy, especially with lean management techniques. This method can significantly boost productivity and efficiency. The real test lies in maintaining this progress over time. Here’s a guide that explores ways to sustain lean management methods for lasting success in any company or group.
Commitment to Continuous Improvement
A key principle in the lean management process is to strive for improvement, promoting a culture that values constant evaluation and refinement of processes within organizations. Established procedures should be regularly assessed to identify inefficiencies and opportunities for development. Seeking input from individuals at all levels fosters a range of perspectives in the enhancement journey.
Maintaining high levels of employee engagement is essential for upholding effective work practices within an organization or business setting. When team members feel their contributions are appreciated and believe they have a stake in the operations and decision-making processes of the company or team, they are more likely to show commitment and dedication to their roles. Encouraging team members to share their thoughts and suggestions can promote teamwork and pave the way for creative solutions to challenges faced by the organization.
Leadership’s Role in Sustainability
The longevity of lean management practices is greatly influenced by leadership qualities. Leaders play a critical role in upholding and exemplifying lean principles for their teams to emulate effectively. By demonstrating a commitment to ongoing enhancement and minimizing inefficiencies, leaders motivate their staff to adopt these principles wholeheartedly.
Effective communication and leadership are crucial for sustaining momentum on this journey within teams. A consistent flow of updates on achievements and acknowledgment of milestones helps keep team members engaged and committed to the process. Additionally, addressing challenges promptly prevents minor issues from escalating into major hurdles and fosters a culture of continuous improvement.
Training and Development
Continuous training and development programs are essential to ensure that employees possess the skills and knowledge needed to support lean management efforts effectively. By investing in employee education, organizations not only enhance individual capabilities but also demonstrate their dedication to lean principles.
Employees can acquire skills and effective methods through workshops and seminars. Motivating team members to participate in training sessions and attend industry events introduces them to innovative concepts and strategies that nurture a culture of continuous learning and flexibility.
Standardization and Documentation
Consistency is key to maintaining effective practices over time. Following standardized procedures helps minimize discrepancies and improves productivity, leading to more reliable results. It is crucial to have documentation in place to ensure that everyone comprehends the processes and can adhere to them correctly.
It’s important to keep documentation up to date to capture any changes in procedures and enhancements effectively, benefiting teams and maintaining consistency across the organization.
Embracing Technology
Incorporating technology can greatly enhance lean management initiatives. Automation tools simplify tasks and allow human resources to focus on strategic activities. Data analysis provides valuable insights into performance metrics and aids in identifying patterns and areas that require improvement.
Utilizing software tools that align with principles like project management or workflow optimization significantly enhances productivity. These digital solutions improve communication and collaboration while enabling progress tracking to bolster the longevity of practices.
Fostering a Lean Culture
Fostering a culture of efficiency and quality within an organization involves integrating lean principles into its core values and day-to-day functions. This promotes employee dedication to enhancing efficiency levels and customer satisfaction.
Recognizing and celebrating wins—whether for individuals or teams—is essential to emphasize the significance of lean management practices and principles. This positive acknowledgment serves as motivation for dedication to lean methodologies and creates an atmosphere of continuous enhancement.
Adapting to Change
The business landscape is always evolving. It is important to be able to adapt in order to maintain lean management practices that can endure. Promoting a positive attitude toward change helps teams prepare for obstacles and devise solutions before they escalate into major problems. Regular evaluations and adjustments to lean strategies in alignment with the company’s objectives and market dynamics bolster resilience and long-term success.
Conclusion
Maintaining a lean management approach demands a commitment to improvement, adaptability, and dedication over time. Organizations can sustain efficiency and productivity by nurturing a culture that values principles and emphasizes training and growth opportunities. Leadership is crucial in advancing these endeavors by facilitating communication and endorsing strategies. Adopting technology and establishing standardized procedures also contribute to long-term sustainability. In essence, a steadfast focus on lean management principles positions businesses for lasting success in today’s dynamic landscape.