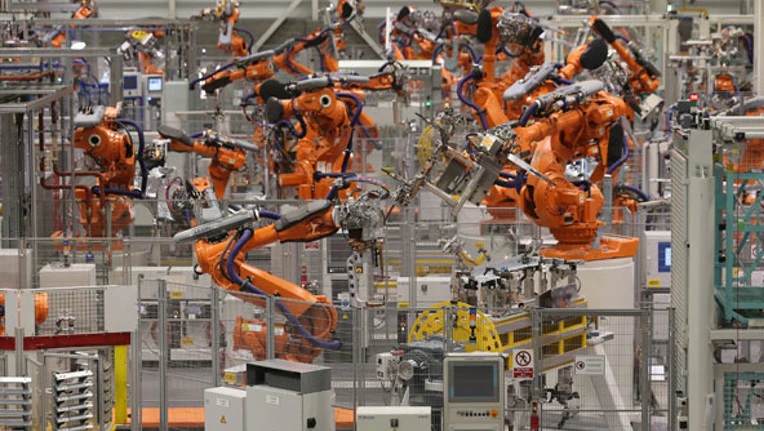
A delay of a few seconds is far from the end of the world in many lines of work. However, any source of delays, pauses or downtime in manufacturing gets amplified across the repetitive nature of production. This has the potential to put a serious wrench in the works, costing companies valuable time and revenue.
Perhaps in no other industry is it quite as important to prioritize productivity and efficiency, and here are three approaches manufacturers are taking in an attempt to do just that.
Automate Certain Processes via “Cobots”
Rather than treating automation as an all-or-nothing proposition, many manufacturers have gone the route of streamlining operations using a combination of employees and collaborative robots (cobots).
Tekedia Mini-MBA edition 16 (Feb 10 – May 3, 2025) opens registrations; register today for early bird discounts.
Tekedia AI in Business Masterclass opens registrations here.
Join Tekedia Capital Syndicate and invest in Africa’s finest startups here.
There are a few potential advantages manufacturers can reap by supplementing their human workforce with robots — precision, 24/7 availability and speed to name just a few.
These gains can also translate into more efficient processes overall.
Five of the key applications for cobots in manufacturing today include:
- Picking items, packing them in boxes and stacking these containers on pallets
- Soldering and welding on an ad hoc basis
- Assembling parts into whole products
- Handling and transporting various materials, including those unsafe for humans
- Inspecting finished products for quality before sending out
Harness Internet of Things (IoT) & Data Analytics
The ever-growing Internet of Things (IoT) is well suited to manufacturing because these smart devices — such as sensors placed all around the manufacturing floor — provide valuable information that decision-makers can then use to make improvements. The proliferation of IoT devices throughout factories and warehouses has gone hand in hand with the rising importance of manufacturing data analysis in making decisions aimed at optimizing business outcomes.
As Industry Week reports, 82 percent of the manufacturing firms that have harnessed the IoT have seen increased efficiency. Similarly, nearly half have reduced the number of product defects and boosted customer satisfaction as a result.
Here’s one example: IoT-connected sensors help manufacturers keep a close eye on equipment usage and reliability — allowing them to intervene quickly when needed and predict when timely maintenance could prevent costly downtime.
Another use case is harnessing IoT to monitor and optimize energy usage within manufacturing facilities — a significant overhead cost that can easily start to climb without intervention. IoT sensors and systems can identify opportunities to reduce waste, replace outdated systems, streamline schedules, proactively schedule maintenance and reduce utility bills.
Streamline Floor Layout
Equipment uptime and energy consumption are important building blocks of overall efficiency, but mean less when floor layout is hampered by lack of flow. As Assembly Mag notes, the arrangement of tools and workstations ultimately affects “ergonomics, productivity and throughput.”
Devotees of the lean manufacturing method, first popularized by Toyota to reduce waste, recommend manufacturing decision-makers take regular “Gemba walks” — an opportunity to step back from normal day-to-day activities to see how everything is flowing. This also gives leaders an opportunity to engage directly with employees on the line, who often have valuable feedback about their workflows and challenges.
While manufacturers may be hesitant at first to reconfigure their lines, doing so with a plan in mind can help maximize flow and minimize waste. For instance, taking the time to reduce extraneous transportation across the factory floor now can shave seconds or minutes off every single batch of finished products in the future. But the key is always basing layout decisions on real worker feedback and data rather than tradition or short-term convenience.
There are many ways to go about improving manufacturing productivity — automation of rote tasks, the use of IoT to beef up data analytics capabilities and optimization of layout are three places to start.